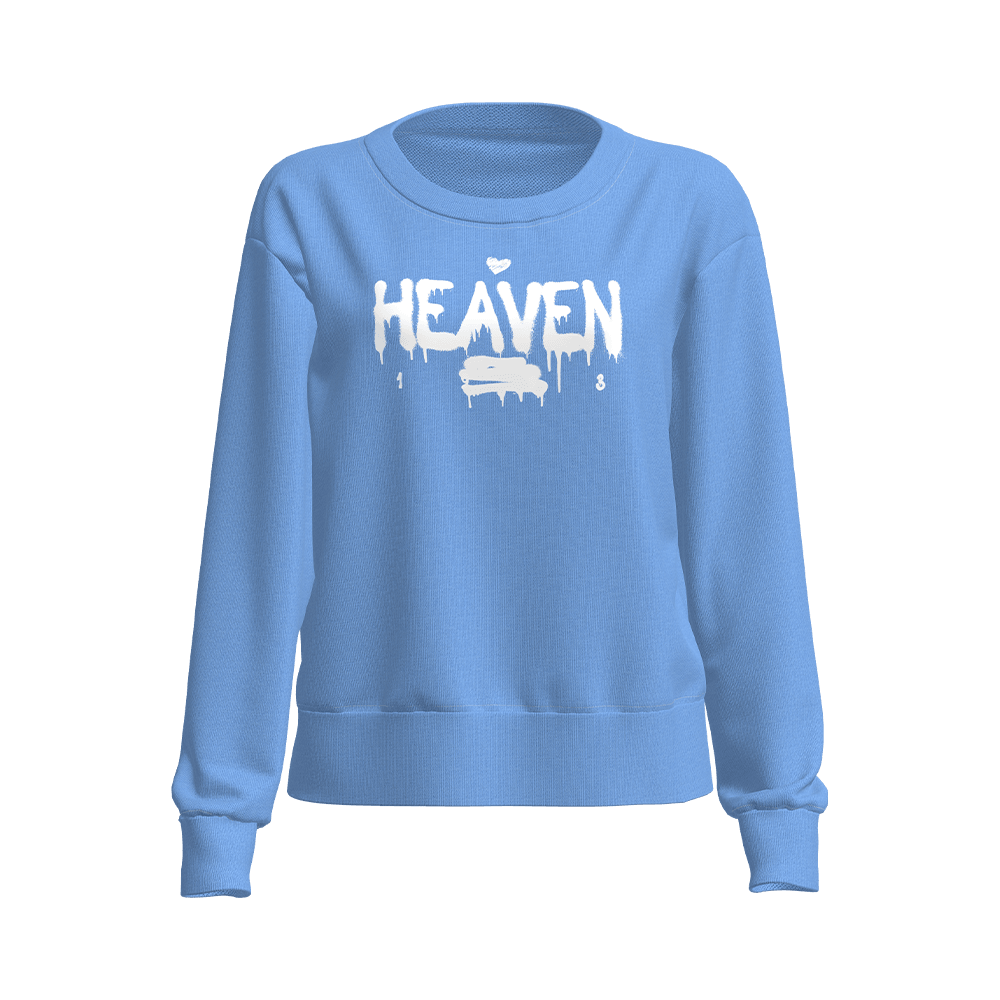
The secret of terry fabric weaving process: the complex process from warp to loops
1. Double warp structure: the basis of terry fabric
The primary difference between terry fabric and ordinary fabrics is that it uses a double warp structure, which gives it a unique terry layer. Usually, the warp and weft yarns of ordinary fabrics are interwoven to form a smooth fabric surface, while terry fabric uses an additional set of warp yarns specifically for the formation of loops during the weaving process.
These two sets of warp yarns play different roles: the ground warp yarn (the first set of warp yarns) is responsible for weaving the basic fabric structure of terry fabric, ensuring the strength and durability of the fabric. The loop warp yarn (the second set of warp yarns) is specifically used to make loops on the fabric surface, which determine the water absorption and softness of the terry fabric. The use of double warp yarns is the technical core of terry fabric, which improves the overall comfort experience by increasing the surface area and softness of the fabric.
2. Formation of loops: a delicate combination of machinery and technology
The weaving of terry fabric relies on complex weaving machinery, which pulls out the loop warp yarns through mechanical devices to form a series of small ring structures, namely loops. The key to this process is how the machine pulls out the warp yarns at specific positions so that they are wound around the needles to form loops. These loops are not completely fixed at the beginning, but need to be finally locked with the help of weft yarns.
The role of the weft yarn is to ensure that the loops can be firmly fixed to the structure of the fabric. After each loop of terry warp yarn is wound into a small loop, the weft yarn will interweave through these loops to stabilize them on the base fabric. In this process, the role of the weft yarn is not only to consolidate the structure, but also to adjust the tightness of the loops, which determines the softness of the loops and the overall feel of the fabric.
3. Loop height and density: key factors affecting fabric performance
The water absorption and softness of terry fabric are mainly affected by the height and density of the loops. During the manufacturing process, the weaving machine can adjust the height of the loops according to different needs. For example, products that require high absorbency, such as bath towels, often use higher loops, while furniture upholstery may use lower loops to increase the durability and ease of cleaning of the fabric.
The density of the loops also determines the feel and functionality of the fabric. High-density terry fabrics are not only softer, but also have better warmth retention and wear resistance. Conversely, lower-density terry fabrics, while more breathable, may be slightly inferior in softness and absorbency. Therefore, when weaving terry fabric, manufacturers usually precisely set the height and density of the loops to optimize their functionality based on the specific product use.
4. Tension control: the core technology to ensure the stability of the loops
Terry warp tension control is an important part of ensuring the quality of terry fabric. If the warp tension is too high, the loops will be pulled too tight, causing the fabric to feel stiff. If the tension is too low, the loops will become loose and easily fall off or lose their shape during use. Therefore, the weaving machine must apply appropriate tension to the warp yarn to ensure that the terry can maintain a soft touch and can be firmly attached to the fabric surface to maintain long-term durability.
5. Post-processing: a key step to enhance functionality and beauty
After weaving, terry fabric usually undergoes a series of post-processing processes to improve its performance and appearance. These processing steps include dyeing, shearing, finishing, etc. The dyeing process not only gives terry fabric a rich color selection, but also enhances its durability and anti-fading properties through chemical treatment. The shearing process can make the terry height more consistent and ensure that the fabric feels uniform.
The finishing process is also particularly important. It not only improves the flatness of the terry fabric, but also increases the softness and antibacterial properties of the fabric through special chemical treatment. For example, high-end bath towels are usually treated with softeners in the finishing process to make the fabric more comfortable to the touch and enhance the user experience.
6. Application and future development of terry fabric
Due to its excellent water absorption, softness and durability, terry fabric is widely used in daily life, such as personal care products such as towels, bathrobes, and bath towels, as well as furniture and home decoration. In recent years, with the increase of environmental awareness, more and more terry fabric produced with organic cotton and environmentally friendly fibers have appeared on the market, meeting consumers' demand for sustainable development.
LATEST POST
Let’s create something amazing together
contact usDon't hesitate to contact when you need us!