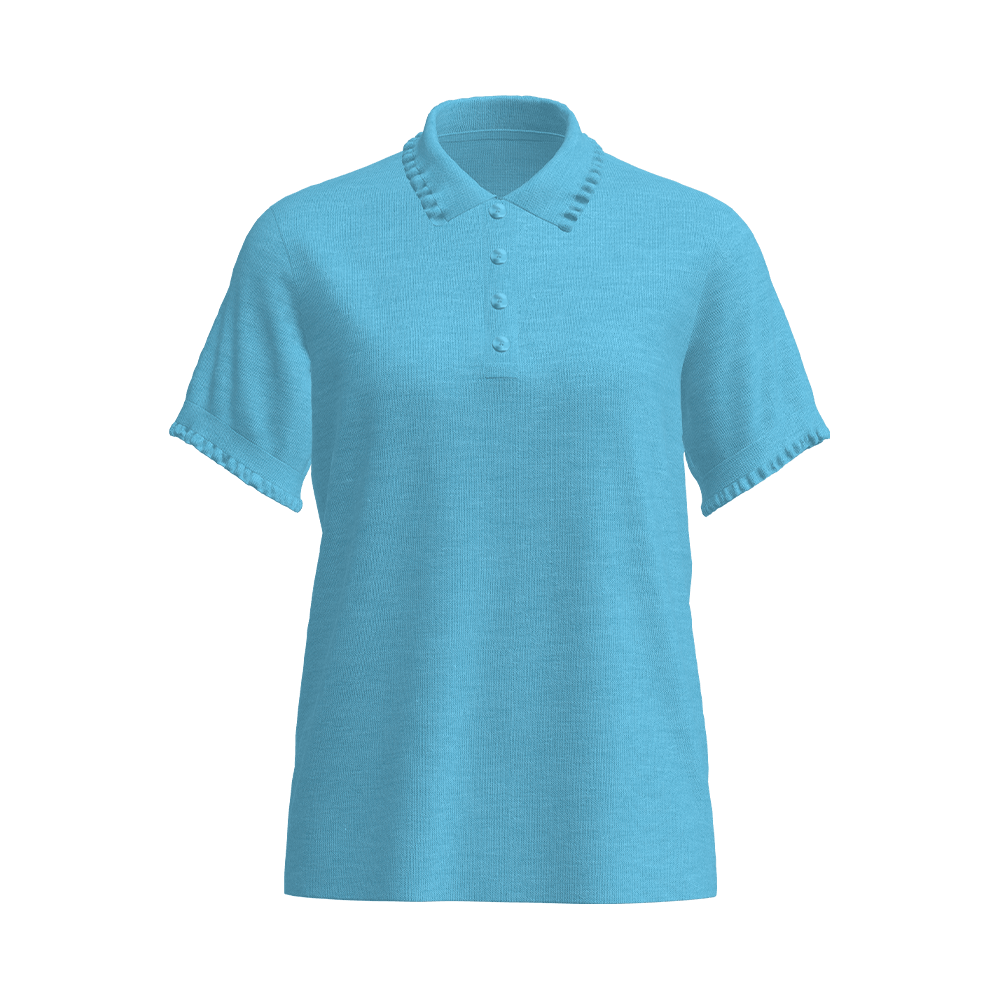
How can anti-static clothing fabrics achieve efficient protection through material selection?
Conductive fiber blending technology is the core technology of anti-static fabrics. By embedding carbon black fiber, metal fiber or copper ion conductive fiber in synthetic fibers such as polyester and nylon, the fabric can form a continuous conductive network. This technology enables clothing to have the ability to quickly transfer charge. When static electricity is generated by human activities, the charge will be introduced into the ground through the fiber network. For example, conductive silk fabrics are made of polyester filaments and high-performance conductive fibers interwoven in warp and weft. After special sewing process, the surface resistivity can be stably controlled within the range of 105-109Ω, achieving a permanent anti-static effect.
The modification of natural fibers takes a different approach. Cotton fabrics can obtain anti-static properties comparable to synthetic fibers by embedding conductive fibers and undergoing anti-static finishing. The principle is that the charge channel formed by the conductive fiber forms a synergistic effect with the hygroscopicity of the cotton fiber-after the cotton fiber absorbs air moisture, the charge transfer efficiency of the conductive fiber is increased by more than 30%. This fabric is widely used in the medical and pharmaceutical fields, which not only meets the cleanliness requirements, but also avoids the skin allergies that may be caused by synthetic fibers.
In flammable and explosive environments, antistatic fabrics must also have flame retardant properties. Polyester-cotton blended fabrics can achieve the dual functions of antistatic and flame retardant by weaving conductive fibers into staple yarns at a spacing of 1.2 cm and finishing them with flame retardant finishing. This fabric is widely used in protective clothing in industries such as petrochemicals and coal mines. Its fabric density is 20% higher than that of ordinary products, which not only prevents static sparks from causing explosions, but also avoids fiber shedding and accumulation of combustibles.
The cleanliness requirements of fabrics in clean room environments are more stringent. Conductive silk fabrics can effectively prevent particles larger than 0.3 microns from attaching due to their dense fiber structure and surface smoothness. After special processing, its surface resistivity can be stabilized at 10^6Ω, ensuring that in scenarios such as semiconductor manufacturing and precision instrument assembly, it not only eliminates the interference of human static electricity on equipment, but also avoids dust generation from the fabric itself.
The fiber weaving process directly affects the uniformity of the antistatic effect. The surface resistivity fluctuation range of fabrics with embedded conductive fibers can be controlled within ±15%, while the anti-static performance of fabrics with surface coatings may be attenuated due to coating wear. For example, anti-static knitted fabrics use knitting technology to tightly combine conductive fibers with polyester filaments to form a three-dimensional conductive network. Even after 50 industrial washings, its anti-static performance can still maintain more than 85% of the initial value.
The post-finishing process also has a significant strengthening effect on fiber performance. After anti-static finishing of all-cotton fabrics, its surface friction coefficient is reduced by 40% and the charge accumulation is reduced by 60%. This treatment not only improves the anti-static effect, but also improves the wearing performance of the fabric - the tingling sensation of the finished cotton work clothes when in contact with the skin is reduced by 70%, making it more suitable for long-term wear.
In the electronics industry, conductive silk fabrics are the first choice because of their excellent dust-proof performance. Its surface smoothness and fiber arrangement density can effectively prevent tiny particles from penetrating, and with anti-static shoes and wrist straps, a complete electrostatic protection system can be built. In the medical field, modified cotton fabrics provide more comfortable protection options for operating rooms and sterile workshops with good air permeability and skin-friendliness.
For chemical environments that need to deal with high temperatures and corrosive gases at the same time, polyester-cotton blended fabrics show unique advantages. Its flame retardant properties can withstand an open flame of 800°C for more than 10 seconds, and the corrosion-resistant treatment of conductive fibers ensures that it can still work stably in strong acid and alkali environments. This kind of fabric can significantly reduce the risk of safety accidents caused by static electricity in chemical storage and transportation, oil refining and other scenarios.
LATEST POST
Let’s create something amazing together
contact usDon't hesitate to contact when you need us!