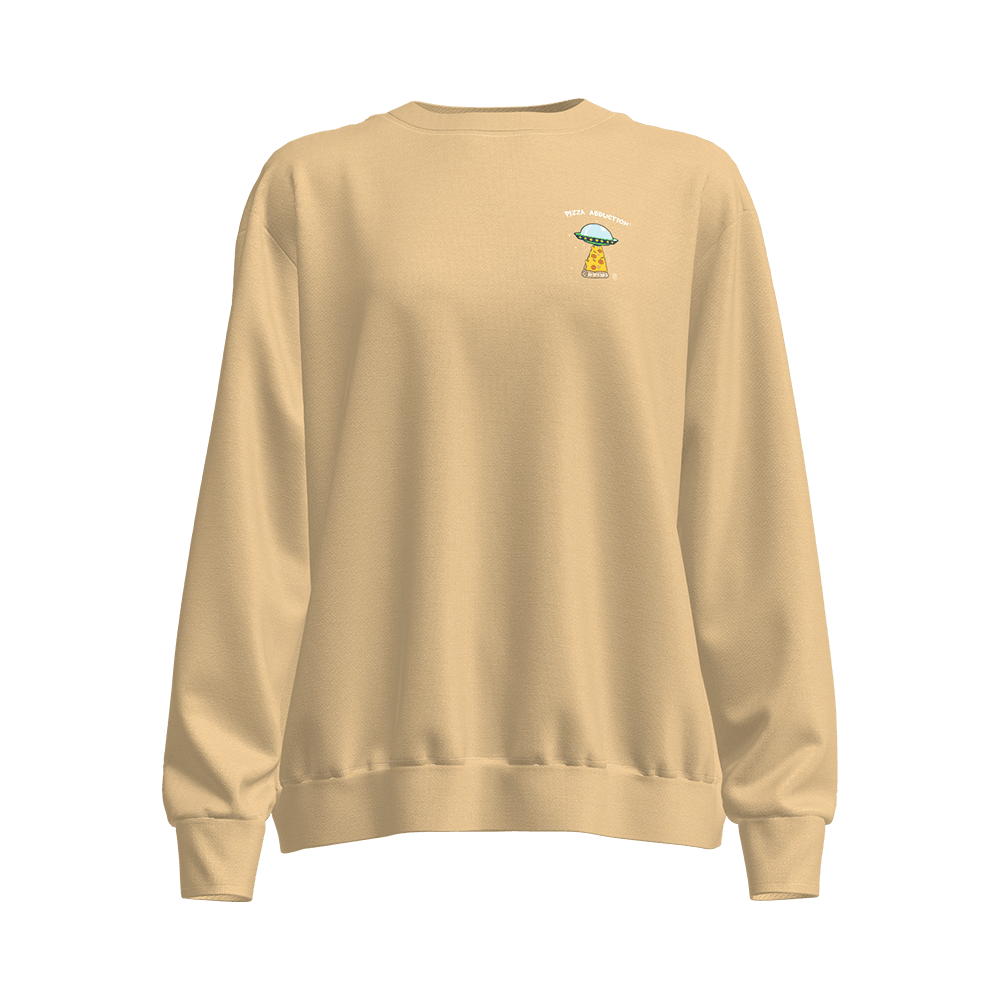
How can thick terry cloth clothing fabric break through the limit of warmth with its structural advantages?
In the field of autumn and winter clothing, thick terry cloth has become the core fabric of sweatshirts, home clothes and other categories with its unique structural characteristics and excellent warmth performance. Its warmth retention is not a simple superposition of the performance of a single fiber, but a three-dimensional structure with both lightness and heat insulation is constructed through the synergy of fiber combination, fabric organization and finishing process. This structural advantage not only reshapes the performance boundary of thermal insulation fabrics, but also promotes the iterative upgrade of autumn and winter clothing towards functionalization and comfort.
The warmth retention of thick terry cloth is based on the scientific design of fiber combination. In traditional crafts, polyester filament, polyester/cotton blended yarn or nylon yarn is often used as ground yarn, while cotton yarn, acrylic yarn, polyester/cotton blended yarn, etc. constitute the terry layer. This two-component structure achieves efficient warmth retention through the "wicking-heat storage" synergistic mechanism: the shaped cross-section fibers in the ground yarn (such as triangular HOY polyester filaments) use the wicking effect to quickly conduct moisture from the body surface to the outer layer, while the hydrophilic fibers in the terry layer (such as cationic modified polyester) disperse moisture through capillary action to avoid heat loss caused by local moisture.
In recent years, the introduction of new fibers has further improved the warmth retention performance. Taking sports sweater fabrics as an example, its terry layer uses fine denier high f-number shaped hollow cross-section polyester DTY. The higher the f-number, the greater the air retention between the fibers, forming a stable insulation layer; the hollow structure reduces the fiber density, making the fabric 20% lighter at the same thickness. In addition, the application of light-absorbing and heat-generating functional fibers (such as ceramic microparticle-modified polyester with infrared absorption characteristics) can convert ambient light energy into heat energy, allowing the fabric to continue to heat up without external friction.
The fabric organization design of thick terry cloth directly determines the upper limit of its warmth retention performance. Double-sided terry cloth forms evenly distributed annular yarn loops on both sides of the fabric through the combination of flat needle coils and terry coils. This three-dimensional structure not only increases the thickness of the air layer between the fibers, but also improves the compression resilience of the fabric through the elastic deformation ability of the terry. Experiments show that the thermal resistance of double-sided terry cloth with the same gram weight is 15% higher than that of single-sided structure, and it can still maintain more than 90% of the initial thickness after repeated compression.
The control of terry height is the key to fabric organization optimization. By adjusting the lateral displacement distance of the comb bar, the terry height can be accurately controlled within the range of 2-5mm. When the terry height is 3.5mm, the fabric reaches the best balance point of warmth and moisture permeability: at this time, the thickness of the air layer can effectively block heat conduction and achieve moisture diffusion through the gaps between the terry loops. In addition, the regularity of the terry distribution is crucial to the formation of the pattern effect. For example, jacquard terry cloth is covered with terry loops with a specific pattern, which gives the fabric a unique visual layering while ensuring warmth.
The finishing process is the core link for the performance advancement of thick terry cloth. The fleece treatment forms fine fluff on the surface of the terry loop through mechanical friction. When the length of the fluff is controlled at 0.5-1mm, the soft touch and fluffiness of the fabric can be significantly improved, while reducing heat loss. The polarization process uses hot air to curl the fiber ends into balls, forming a heat storage unit similar to down, which increases the warmth of the fabric by 20% while reducing the thickness by 10%.
The introduction of coating and film technology has brought more possibilities to thick terry cloth. Nano-ceramic coating can increase the far-infrared emissivity of the fabric to 0.92, enhancing its light absorption and heat generation performance; while the composite of hydrophilic polyurethane film gives the fabric a unidirectional moisture conduction function, allowing the moisture on the body surface to be quickly discharged through the fabric while preventing external water vapor from penetrating. These finishing processes not only improve the warmth retention of the fabric, but also expand its application scenarios in outdoor sports, medical protection and other fields.
The structural advantages of thick terry cloth are directly converted into multi-dimensional performance improvements. In terms of warmth retention, the thickness of its air layer can reach 2-3 times that of ordinary knitted fabrics, and the thermal resistance value (CLO value) is usually between 0.5-1.2, which can cope with the temperature range of -5℃ to 15℃. In terms of moisture permeability, the capillary channels of the terry structure keep the fabric moisture permeability above 3000g/m²·24h, ensuring that the wearer's body surface is dry.
In terms of comfort, the elastic recovery rate of thick terry cloth can reach more than 95%, and it can still restore its original shape even after strenuous activities; the anti-pilling performance reaches more than level 4, and the appearance retention rate after 50 washes exceeds 90%. In addition, through fiber modification technology, the fabric can realize the integration of antibacterial, antistatic, and UV protection functions. For example, the antibacterial rate of silver ion modified polyester terry cloth against Staphylococcus aureus exceeds 99%.
LATEST POST
Let’s create something amazing together
contact usDon't hesitate to contact when you need us!