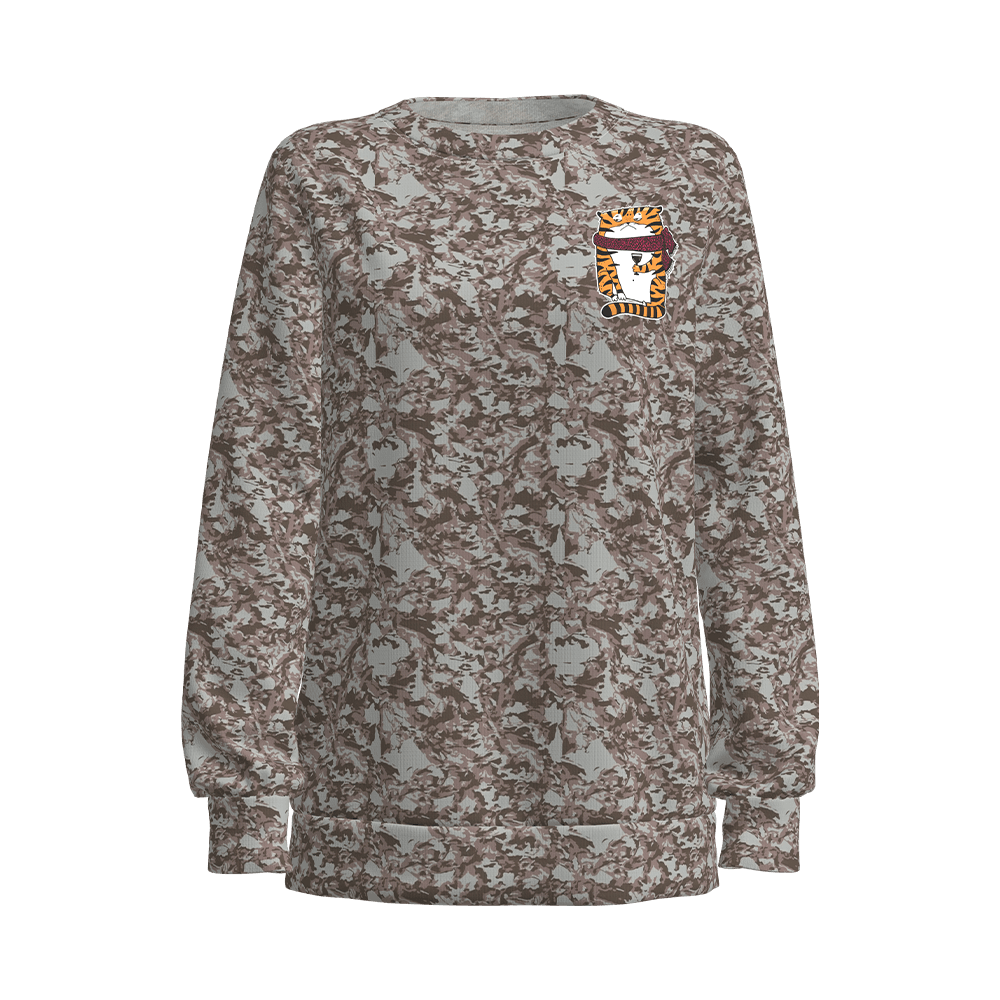
How to create high-quality digital printed French terry cloth?
The first step to create high-quality digital printed French terry cloth is to choose high-quality fiber raw materials. Common raw materials include cotton, polyester and blended materials.
Cotton: Cotton fiber is an ideal choice for making terry cloth due to its good moisture absorption, breathability and skin-friendliness. High-quality cotton fibers, such as long-staple cotton, have long fibers, high strength and good softness, which can give terry cloth a better feel and durability.
Polyester: Polyester fibers also play an important role in the production of terry cloth due to their wear resistance, wrinkle resistance, easy washing and drying. High-quality polyester fibers, such as ultra-fine denier polyester, have a finer fiber diameter and can form a more delicate and soft terry structure while maintaining the stiffness and elasticity of the fabric.
Blended materials: Blending fibers such as cotton and polyester can make full use of the advantages of various fibers and form complementary advantages. For example, cotton-polyester blended materials combine the comfort of cotton and the durability of polyester, making them the preferred choice for making high-quality terry cloth.
When selecting fiber raw materials, in addition to considering the performance of the fiber itself, it is also necessary to pay attention to the origin, grade and batch stability of the fiber. High-quality fiber raw materials are the basis for creating high-quality digital printed French terry cloth.
With high-quality fiber raw materials, the next step is to weave these fibers into a fabric base with a terry structure through a precise weaving process.
Weaving equipment: In the modern textile industry, advanced weaving equipment is the key to achieving precision weaving. The use of high-efficiency equipment such as high-speed rapier looms and air-jet looms can ensure the precise arrangement of yarns and the uniformity of fabrics.
Weaving parameters: During the weaving process, it is necessary to strictly control parameters such as yarn tension and weaving density. The size of the yarn tension directly affects the shape and stability of the terry. If the tension is too large, the terry is easy to be straightened, affecting the thermal insulation performance; if the tension is too small, the terry is loose, affecting the beauty and durability of the fabric. The weaving density determines the thickness and breathability of the fabric. If the density is too high, the fabric is thick and heavy, and the breathability is poor; if the density is too low, the fabric is thin and the thermal insulation performance is insufficient.
Terry structure: Terry structure is the core feature of digital printed French terry. By adjusting the warp and weft interweaving method, terry height and other parameters in the weaving process, different styles of terry structures can be formed, such as plain terry, twill terry, double terry, etc. These different terry structures not only affect the appearance and feel of the fabric, but also directly determine the warmth retention and durability of the fabric.
In the production process of digital printed French terry, in addition to the selection of fiber raw materials and the optimization of weaving process, the production parameters need to be precisely controlled to ensure the uniformity and stability of the fabric.
Yarn pretreatment: Before weaving, the yarn needs to be pretreated, such as sizing and waxing, to improve the strength and wear resistance of the yarn, while reducing the friction and breakage of the yarn during the weaving process.
Tension control system: Modern weaving equipment is usually equipped with an advanced tension control system that can monitor and adjust the tension of the yarn in real time to ensure the stability and consistency of the yarn during the weaving process.
Density detection and adjustment: During the weaving process, the density of the fabric needs to be regularly detected and adjusted. By adjusting the warp and weft density controller of the loom, the density of the fabric can be ensured to meet the design requirements, thereby ensuring the thickness, breathability and warmth of the fabric.
Terry height control: Terry height is one of the key factors affecting the warmth and appearance of the fabric. By adjusting the terry height controller in the weaving process, the height and shape of the terry can be accurately controlled to meet the needs of different customers.
In the production of high-quality digital printed French terry cloth, digital printing technology undoubtedly adds fashion and personalization to it.
High-precision printing: Modern digital printing equipment uses high-precision nozzles to print the design pattern on the fabric with pixel-level accuracy. This high-precision printing technology not only ensures the clarity and delicacy of the pattern, but also makes the pattern on the fabric more vivid and three-dimensional.
Color management: Digital printing technology uses an advanced color management system that can accurately restore the colors in the design pattern. Through precise color matching and calibration, it can ensure that the color of the pattern on each piece of fabric is consistent with the design draft, thereby meeting the color needs of customers.
Personalized customization: Digital printing technology also gives fabrics the ability to be personalized. Customers can customize unique patterns and color combinations according to their preferences and needs, making each piece of fabric a unique work of art.
In the production process of high-quality digital printed French terry cloth, quality inspection and certification are important links to ensure product quality and reputation.
Physical performance testing: Physical performance tests are conducted on the produced fabrics, such as tensile strength, tear strength, abrasion resistance, breathability, warmth retention, etc., to ensure that the fabrics meet the design requirements and usage standards.
Chemical performance testing: Chemical performance tests are conducted on the fabrics, such as formaldehyde content, pH value, color fastness, etc., to ensure that the fabrics meet environmental protection requirements and safety standards.
Quality certification: Certification by international authoritative certification agencies such as ISO9001 quality management system certification and OEKO-TEX ecological textile certification can further enhance the quality and reputation of the products and enhance customer trust and satisfaction with the products.
LATEST POST
Let’s create something amazing together
contact usDon't hesitate to contact when you need us!